The evolution of mine door actuation
Mining has been around for thousands of years. Like most industries, mining evolved throughout the industrial revolution time period. Mines became more efficient, and more productive. In time, mines went deeper underground requiring additional ventilation fans and mine doors for controlling airflow. A hundred years ago the mines relied on “trappers” to stand by the mine doors to manually open and close the doors for approaching mule/hauling carts and other mining equipment. Eventually this evolved into mechanized actuation of mine doors.
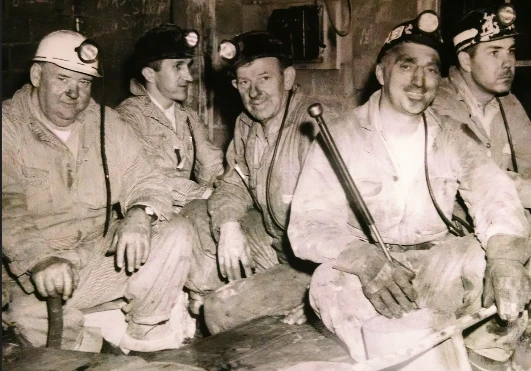
In the beginning was Mechanized Actuation
The first attempt to automate mine doors was a clever design using the energy created by a train traveling down the railroad tracks. Through a series of latches, gears, and levers, the energy created by the traveling train opened and closed the doors . The photo to the left shows a description from an early American Mine Door (AMD) brochure retrieved from our archives.
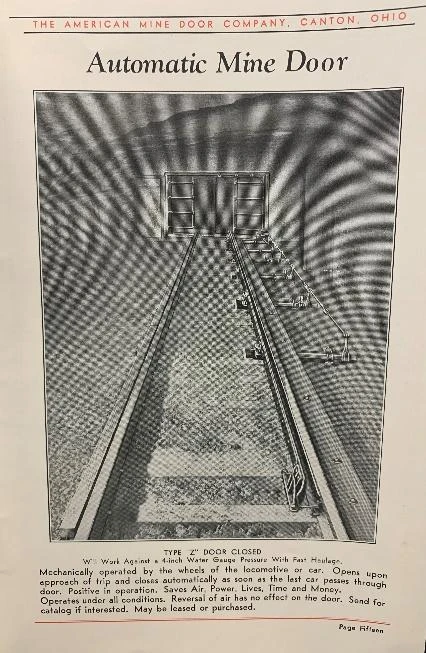
Next Came Pneumatic Actuation
Air cylinders under compressed air were used to drive the opening and closing of mine doors. AMD introduced pneumatic actuation in the early 1900’s and it is still being purchased by mines today.
The AMD Pneumatic Control Systems include a single air cylinder that is installed on top of the doors. The systems operate with a pressurized air supply and require a minimum of 120 PSI to operate the doors actuation. Pressurized air travels into a 2-way directional valve. When a pull switch is activated, this signal travels to the solenoid and directs the cylinder valve to either the open or closed position.
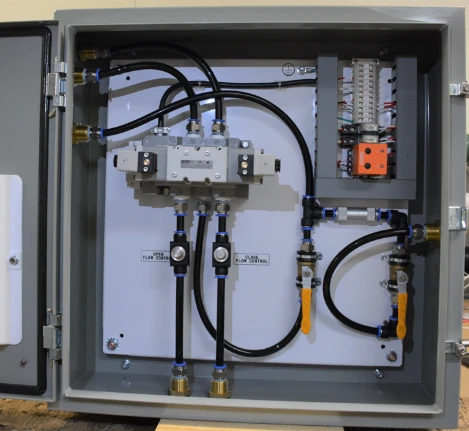
Hydraulic Actuation became the “Tried and True” Solution
Over the years, mines went deeper and deeper underground. More powerful fans were required and higher air pressures followed. In addition, mine doors grew larger to accommodate larger haulage vehicles and other mining equipment traveling through the ventilation doors. Increasing the psi output to pneumatic system was not always a safe solution. Compressed air acts like a spring under pressure. To avoid this “spring effect”, the better choice for safety became hydraulic (non-compressable) actuation.
Out of necessity a safer hydraulic actuation of mine doors was required in these high-pressure applications. AMD acted and introduced hydraulic actuation in the mid 1900’s to meet these new demands. Hydraulics offered a safer, more robust actuation system that offered more output force and torque which is required for opening larger ventilation mine doors under greater air pressure.
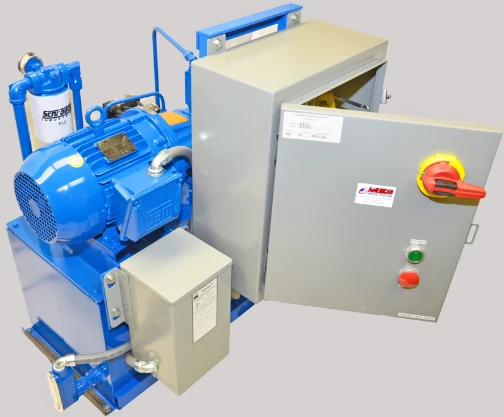
AMD’s Hydraulic Power Unit (HPU) is a self-contained hydraulic system complete with a hydraulic cylinder, electrical controls and safeties. Most come with a 20-gallon reservoir, a 1-gallon accumulator, 3 HP to 5 HP motor (any voltage), 6 gpm vane pump, suction strainer, tank heater, relief valve, pressure gauge, manifold, valves, return line filter, pressure switch, with 1/2″ diameter 50′ long mine rated hydraulic hoses.
The Rise of All Electric Actuation
Electric Mechanical Actuators became “the thing” in recent years. They offered ease of control and were easy to configure. Electric Actuators can boast of greater efficiencies by offering energy efficient servo drives and power on demand that saves energy costs for the mine.
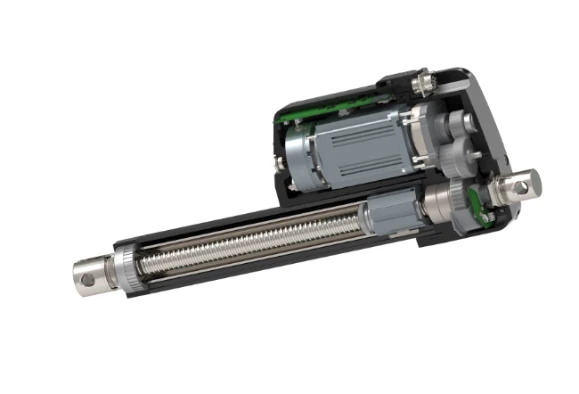
In addition, network connectivity and diagnostics offered real advantages for those mines that are monitoring and controlling vent doors topside.
Yet electric actuation in mining offered several real-world challenges for mines. The screw type Electric Actuators are designed with metal-to-metal wear that you do not get with pneumatic and hydraulic actuation. The roller & ball screw actuators are complex and wear out prematurely.
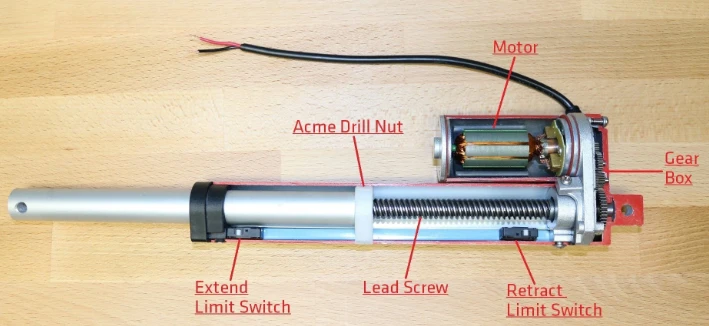
This metal-to-metal friction reduces efficiency and life span. Also, the force-density is lower than a Hydraulic Actuator; thus the actuator must be oversized to extend life.
AMD also experienced that the All Electric Screw Type were susceptible to damage by initial shock loads when opening and closing doors. They also require frequent lubrication to extend the service life. This is not often easy to do underground.
The Next Generation of Mine Door Actuation
Both hydraulic, and electric actuation systems have their advantages and disadvantages. What if you can combine the best of both worlds? …AMD went to work.
Over the last several years AMD has researched and developed an actuation system that can combine the efficiency of electric actuation and the robustness of hydraulics. The wait is over. With hundreds of hours of research and development, AMD is now offering a revolutionary hybrid electric hydraulic actuation solution second to none.
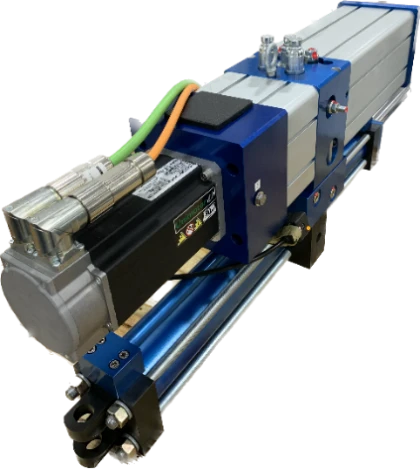
AMD introduced the system several years ago and is well beyond proof of concept and field testing. Presently, international high-tech modern mines are incorporating the AMD hybrid electric-hydraulic actuation system. They are taking advantage of the best of electric and the best of hydraulic actuation into one AMD Hybrid Mine Door Actuator. These actuators amazingly offer high output forces (up to 85,000 lbf / 377 kN) in a very small footprint. These actuation systems are being monitored and controlled with precision from topside network connectivity.
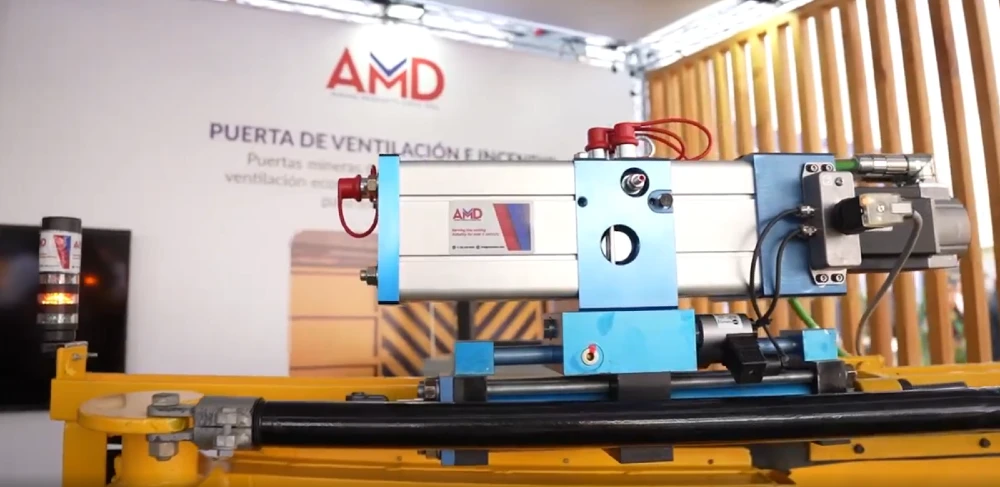
The AMD hybrid actuators are a combination of electro-mechanical actuators and traditional hydraulics while eliminating the shortcomings. These units incorporate a self-contained hydraulic pump and hydraulic cylinder into one compact package. A high technology servo drive is housed inside the control cabinet that monitors and controls the actuator. They easily allow for speed and pressure adjustments. When received at the mine site, the units are ready to install. The units arrive on-site prefilled with hydraulic fluid at the factory. The unit attaches to the mine door using two (2) clevis pins and requires only three (3) cables to the control system.
It is essentially an “electric actuator” that looks similar to a screw-type actuator but rather than using gears, drive screws and driven nuts, the AMD Hybrid uses an integral hydraulic cylinder with a minimum of 94 ounces (2.8 Liters) of fluid.
Currently AMD Hybrid Actuators are being used in some of the harshest mine environments around the world. Requires no hydraulic hoses, no threaded connections, no leaks from hoses or fittings, no fluids to install, no containment pads, no nitrogen filled accumulators.
- A smarter solution to pure electric actuators removing the risk of damaged screws from shock loads, premature wear, intermittent reliability, and potential high maintenance costs.
- A smarter solution to pure hydraulics eliminates excessive hydraulic hoses with no risk of hydraulic leaks. Saves energy by eliminating the constant running of Hydraulic Power Units (HPU) with little to no footprint.
The AMD Hybrid Actuator has a programmed Servo Drive that is housed in the AMD PLC Control Cabinet. It offers precision control for monitoring and operating the door at the mine door location or remotely above ground. The AMD Hybrid offers versatile configurations, accurate control and fieldbus connectivity like never before.
The AMD Hybrid is taking the mining industry by storm. It is an ideal solution for the AMD Patented Opposing Wing Design Mine Door. Only one actuator is required for the AMD mine door.
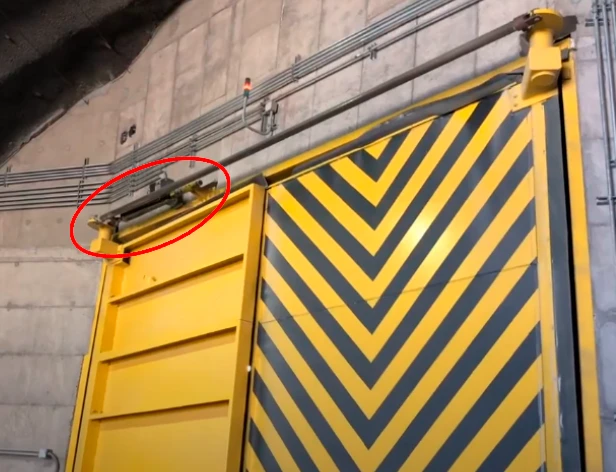
Each actuator is engineered for the proper force, torque and electrical power requirements for each unique ventilation mine door system.
The AMD hybrid actuators offer high output forces (up to 85,000 lbf / 377 kN) in a very small footprint.
Breakthrough Performance Results of the AMD Hybrid Actuator
- Energy efficiencies and performance
It is well known that energy consumption for ventilation is one of the most expensive ongoing daily operations costs for running a mine. The reduced energy consumption with Power on Demand control is a real game changer. Findings have shown that the AMD hybrid actuators are 340% more efficient to operate vs. a comparable output of a traditional hydraulic system.
The is no compromise with performance force demands. The AMD Hybrid can go toe-to-toe with traditional hydraulic units in maintaining force. The AMD hybrid actuators offer high output forces (up to 85,000 lbf / 377 kN). They are one of the most energy efficient actuation options available today.
- Environment Impact
Dirt and dust from traditional hydraulic systems can damage or wear hydraulic components very quickly. The AMD Hybrid’s sealed all-in-one system is leak-free and environmentally clean. AMD hybrid actuators never require hydraulic fluid changes. The actuator only requires 94 oz (2.8 Liters) of hydraulic fluid that is filled at the factor in a clean room environment. Hydraulic fluid options are available with non-flammable, and non-freezing fluid. In short, has minimal environmental impact at the mine.
- Employee Safety
It is important to note that AMD hybrid actuators have very little “stored energy” like traditional hydraulics do. When an AMD Hybrid Actuator is shut off, most of the pressure in the actuator is released. Will store approximately ~ 5psi when fully extended to ~15psi when retracted. This significantly lessens the potential for injury when doing maintenance. Traditional HPU’s run at high pressures. There is potential for bursting hoses or fittings. The AMD hybrid actuators are installed at the top of the mine door. A complete self-contained unit; that is it.
- Economic Consideration
Lower in cost than traditional hydraulics (initial cost and life of product cost). The AMD hybrid actuator requires no maintenance for 8000 hours. At 150 cycles/day at 24 seconds per cycle. Operating 24/7 & 365 days = ~18 years of service without any required maintenance.
After 8000 hours of operation, these actuators can be rebuilt (new seals, new pump and hydraulic fluid are replaced) for a fraction of the cost of a new actuator. The actuator is rebuilt in a clean room and tested before returning to the customer. A rebuilt actuator offers an additional 8000 hours of operation along with a new warranty!
5. Simplistic Design
Using a self-contained actuation system lessens complexity compared to a traditional hydraulic system. Less complexity means less maintenance, less components to fail, less cost, and less downtime. A traditional HPU requires fluid to be installed outside of a clean room, allowing the potential of dirt or dust to enter the hydraulic system. Contaminated fluid can wear or damage internal components. A traditional HPU has many more components than an AMD hybrid actuator such as pressure gauges, flow valves, manifold, pressure switches, accumulators, control systems and disconnects, complex pumps, filters, heaters, hydraulic tubing, screw type fittings, and hoses.
Summarizing the Most Reliable and Efficient Mine Door Actuation System on the Market Today
AMD will program and test each hybrid Actuator at the factory to the proper pump pressure, output force and door open/close cycle speeds. Requires only communications cable, power cable and solenoid cable. No hoses to install. No fluids to add. This significantly reduces complexity and time spent on installation as an All-In-One plug-and-play system. The AMD Hybrid Actuation System can withstand the most demanding shock loads for high pressure ventilation mine doors with no metal-to-metal wear.
In summary, this All-in-One Hybrid Actuation solution makes the complex simple and versatile. The total cost of ownership is drastically reduced with minimal upfront costs, simpler installation, reduced operating energy cost, and environmentally clean actuation with precise control. The AMD Hybrid is the most reliable and efficient actuation system on the market today.
Come see it at MINExpo
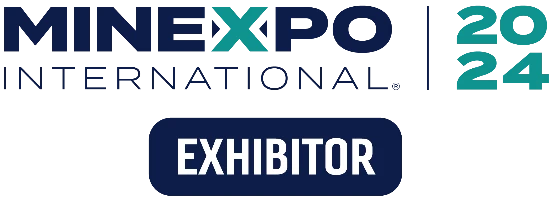
The AMD Hybrid Actuator will be displayed at the upcoming MINExpo 2024 International Mine Trade Show in Las Vegas Nevada from Sept 24th through Sept 26th.
For a demonstration stop by the MINExpo International Trade Show. AMD will be in the West Hall, Booth #11600 . See if this solution is right for your upcoming project application. If you cannot attend contact AMD for more information.
The imagery and content of this brochure is for marketing purposes only. Please contact AMD with questions regarding your exact specifications.